магазин
stirred mill grinding
KEFID,Дробильно-сортировочное оборудование Китая высокого качества, стандартное дробильное оборудование. На протяжении более 30 лет мы занимаемся исследованиями и разработками и производством дробильного оборудования, дробления зданий, промышленных дробилок и экологически чистых строительных материалов, и предлагаем профессиональные решения и дополнительные продукты для создания ценность для клиентов.
Онлайн сообщение
stirred mill grinding

Stirred mills for milling & grinding |
Stirred mills & Tower mills — simple, effective and cost efficient As lower ore grades and complex mineralogy are driving demand for more efficient fine grinding, you can depend on for a full range of finegrinding mills designed for easy shipment, simple erection and troublefree maintenanceStirred media Detritor (SMD) is a fluidized, vertical stirred mill designed for optimum grinding efficiency for fine and ultrafine grinding products SMD’s feed size is typically 80% passing 100 µm and finer, but it can also handle coarser materials in various applicationsStirred mills for wet grinding minevik
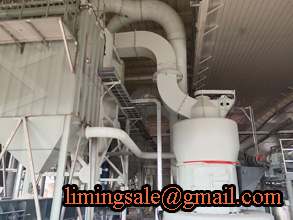
Stirred Mill an overview | ScienceDirect Topics
Different kind of mills are suitable for grinding, mechanical alloying and mechanical milling such as horizontal mills (tumbler ball mill), stirred mill (attritor, eg Szegvari attrition mill 1), planetary ball mill, vibrating mill (tube vibrating mill, Sweco vibrating mill and shaker vibrating mill (eg Spex is a labscale mill 3))Their working principles and operating conditions areJun 01, 2020· Stirred media mills Efficient grinding of fine and ultrafine particles requires small media to increase the surface area and the consequent collision frequency, but ball mills are fundamentally limited in the momentum that can be applied to such small beads by the force of gravity, which sets a practical lower limit in media sizeStirred media mills in the mining industry: Material
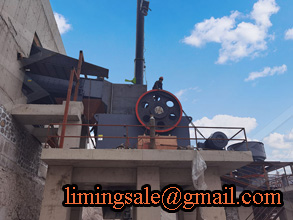
Stirred Media Detritors (SMD) minevik
Stirred Media Detritor (SMD) is a fluidized, vertical stirred mill designed for optimum grinding efficiency for fine and ultrafine grinding products SMD’s feed size is typically 80% passing 100 µm and finer, but it can also handle coarser materials in various applicationsFig 1 Vertical stirred media mill (Outotec, 2012) Principle of operation The mill feed is pumped to the grinding chamber via the feed inlet at the bottom of the mill During continuous operation, the slurry flow transfers upwards and passes through the rotating discs and intoStirred Milling Technology – A New Concept in Fine Grinding
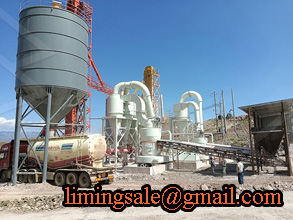
Stirred milling—new comminution J technology in the PGM
Stirred milling—new comminution technology in the PGM industry production processes; ultra fine grinding of industrial minerals; and in the pharmaceutical, food, printing inks, ceramic and chemical industries The first applications of stirred mills in the metals mining industry occurred in the lead and zinc industry with the– Horizontal, high intensity stirred mill > high energy efficiency – Inert grinding environment > selective flotation, high recovery – First fullscale IsaMill installed Pb/Zn circuit Mount Isa, 1994 – Enabling technology for McArthur River, 1995STIRRED MILLING TECHNOLOGY XPS

Stirred milling—new comminution J technology in the PGM
Stirred milling—new comminution technology in the PGM industry production processes; ultra fine grinding of industrial minerals; and in the pharmaceutical, food, printing inks, ceramic and chemical industries The first applications of stirred mills in the metals mining industry occurred in the lead and zinc industry with theAbstract Stirred mill technology dates back to 1928 where the idea to use "an agitator and spherical grinding media" was presented In the context of the mining industry, interest in stirred milling technologies has grown over the last 20 years where the typical observation reported in the literatuStirred Milling CEEC (Coalition for Eco Efficient
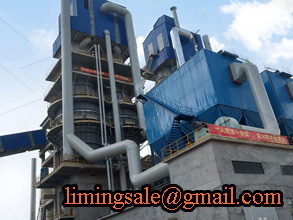
STIRRED MILLING TECHNOLOGY XPS
– Horizontal, high intensity stirred mill > high energy efficiency – Inert grinding environment > selective flotation, high recovery – First fullscale IsaMill installed Pb/Zn circuit Mount Isa, 1994 – Enabling technology for McArthur River, 1995The horizontal stirred mill approach for grinding rocks, minerals, and industrial materials was developed in Australia, where it has been used for a number of years Conventional ball mills rotate the mill body (a horizontal cylinder), tumbling both rock and metallic balls Stirred mills use an internal auger to agitate the feedstock (ore whichFine Grinding Technology for Mines and Concentrating
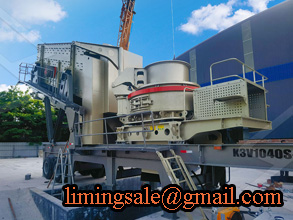
Stirred Media Detritor SMD1100E Circuit Animation
Oct 05, 2015· The Stirred Media Detritor (SMD) is a fluidized, vertical stirred mill designed for optimum grinding efficiency for fine and ultrafine grinding products The SMD utilizes the rotational energy ofThe knowledge of physical phenomena inside the mill and industrial applications have significantly increased in the last 15 years This course gives an overview about the current mill design available on the market and about the the physical phenomena of grinding and dispersing in stirred media millsGVT Grinding and Dispersing Online
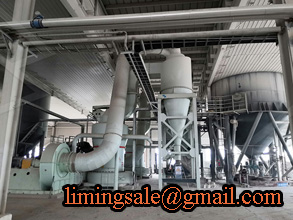
Stirred Milling machine development and application extension
Gravity induced screw stirred mills •TypesVERTIMILL® (VTM)Eirich Tower mill™ • General characteristicsGravity keeps media in the millCharge weight aids grindingLow intensity, low tip speedHigh density mediaMedia sizes 38 –5 mmScrew agitator to lift charge 5 13 Nov 2013Apr 25, 2013· AG or SAG mill, intermediate grinding to a ball mill or tower mill, and fine grinding to a stirred mill such as an Isamill or Stirred Media Detritor (SMD) Of course, various exceptions to these typical values can be found In fine grinding, a material with an F80 of less than 100 lm is comminuted to a P80 of 7 to 30 lm (P80s ofEnergy Use of Fine Grinding in Mineral Processing
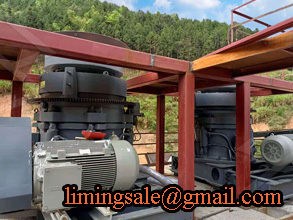
Grindforce Back to Basics Outotec
The particle grinding mechanism in stirred milling is almost 100% attrition or shear type grinding, , rather than impact grinding as occurs in tumbling mills, like SAG and ball mills Large particles (> 1 mm) can be efficiently reduced in size by impact grinding where the breakage method is shattering of particles by direct fall upon them fromThese features distinguish stirred mills as fundamentally different from both ball mills and Tower Mills, as demonstrated by Tables 1 and 2 Table 1 : Typical Power Intensities of different Grinding Devices Table 1: Power Intensity of Different Grinding Devices Ball Mill is a 56m D x 64m L @ 26MW Tower Mill is a 25m D x 25m L @ 520KWFine Grinding as Enabling Technology – The IsaMill
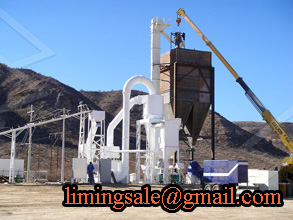
Investigating the Grinding Media Behavior in DryStirred
Dryoperated stirred mills hold promise for energyefficient dry finegrinding operations However, the motion of the grinding bead within this mill type is still not well understood So, the Institute for Particle Technology (iPAT) at Technische Universität Braunschweig recently used Rocky DEM simulation tools to investigate bead contactPrimary or regrinding mill; Ideal for “precision” grinding on finer products; Restriction in feed size (6mm) Restriction in energy (1119 kW/ 15oo hp) Ball size max 30mm; Vertimill by minevik Minerals [image: (135616)] Stirred Mills vs Tumbling Mills Advantages of Stirred Mills (VERTIMILL ®): Lower installation cost; Lower operation costAMIT 135: Lesson 6 Grinding Circuit – Mining Mill Operator

Vertimill® grinding mills & stirred media detritor by
Aug 29, 2013· Typical Grinding Ranges Mill Type Ball Mill Vertimill® SMD 10000 1000 100 10 Microns 1 Ball Mills and stirred mills are applied across aThe popularity of stirred media mills has risen in recent times CITIC HIC has developed our own range of vertical stirred media mills to complement our conventional grinding mills range, research and development team in Australia and CHina constantly working improving technology and efficiency ofVertical Stirred Mills (CITIC Stirred Mills CSM) CITIC

Stirred Media Detritor SMD1100E Circuit Animation
Oct 05, 2015· The Stirred Media Detritor (SMD) is a fluidized, vertical stirred mill designed for optimum grinding efficiency for fine and ultrafine grinding products The SMD utilizes the rotational energy ofAug 29, 2013· Typical Grinding Ranges Mill Type Ball Mill Vertimill® SMD 10000 1000 100 10 Microns 1 Ball Mills and stirred mills are applied across aVertimill® grinding mills & stirred media detritor by

Getting intense about grinding CIM
Stirred mills use attritiontype grinding, which wears away the surface of ore particles instead of breaking them The HIGmill is one of a few vertical designs that let gravity do the work of compacting the grinding media and promoting efficient contacts between media and ore slurryMany papers suggest that HPGR and Stirred Mills are a better alternative to SAG and Ball mills in terms of energy efficiency and mineral liberation Many papers say that the higher CAPEX is compensated by the lower OPEX Why then, do not all mines or at least the majority that are under construction rely on these grinding technologies?Popularity of Stirred Mills and HPGR Crushing, Screening
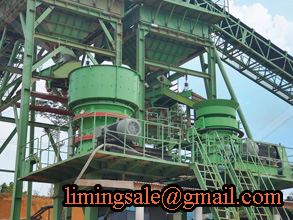
Regrinding and fine grinding technology the facts and myths
The active grinding volume in a stirred mill was first determined by simulation and later investigated by measurements Grinding is a consequence of the velocity gradient between the grinding media and the particles in the slurry which generate stress events The different grayThe IsaMill is a horizontal stirred mill with sizes up to 3 m3 chamber net volume and 1120 kW installed motor It was jointly invented by Mount Isa Mines of Australia and Netzsch Feinmahltecknik GmbH of Germany for ultrafine and fine grinding duties in the minerals industryISAMILL FINE GRINDING TECHNOLOGY AND ITS INDUSTRIAL

CITIC Stirred Media Vertical Mill
Aug 27, 2015· The OK™ mill the most reliable and efficient mill for raw and cement grinding Duration: 2:47 12,835 viewsGrinding Power efficiencies are achieved by 100% filling of charge and smaller steel media (balls) used for fine grinding Typically, stirred media mills use 25mm makeup balls, where conventional ball mills are using much larger grinding media The popularity of stirred media mills has risen in recent timesCITIC STIRRED MILLS (CSM)
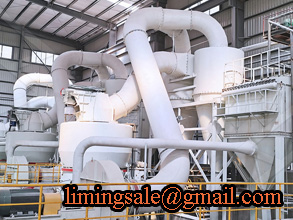
air classifier | powder processing | grinding mills | RSG
The ufg mill® is a dry agitated media mill suitable for producing powders in the range of 40 microns down to 1 micron The feed material is typically below 2 mm and moisture below 1% The ufg mill® is normally operated in closed circuit grinding with a high efficiency air classifierFINE GRINDING—DEVELOPMENTS IN CERAMIC MEDIA TECHNOLOGY 53 Introduction The high energy efficiency of stirred mills compared to ball mills is well understood within the industry The use of tower mills as an energy efficient alternative to secondary and regrind ballFine grinding—Developments in ceramic media technology
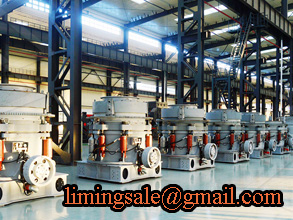
Grindforce Back to Basics Outotec
The particle grinding mechanism in stirred milling is almost 100% attrition or shear type grinding, , rather than impact grinding as occurs in tumbling mills, like SAG and ball mills Large particles (> 1 mm) can be efficiently reduced in size by impact grinding where the breakage method is shattering of particles by direct fall upon them fromStirred Mills – Ultrafine Grinding ScienceDirect Figure 101 shows the difference in energy efficiency between a laboratory ball mill and a stirred mill grindingefficiency of stirred mill
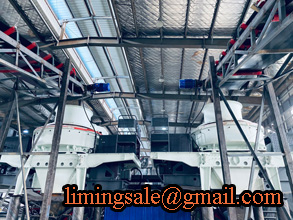
Grinding of Calcite in a Stirred Media Mill Using the Box
The grinding experiments were re alized as a batch process with calcite specimens received from the grinding tank in a detected grindingtime interval All of the media and calcite specimens were detracted from the stirred media mill after each experiment, and the grinding media were separated from the calcite specimens as a result of dry sievingPrimary or regrinding mill; Ideal for “precision” grinding on finer products; Restriction in feed size (6mm) Restriction in energy (1119 kW/ 15oo hp) Ball size max 30mm; Vertimill by minevik Minerals [image: (135616)] Stirred Mills vs Tumbling Mills Advantages of Stirred Mills (VERTIMILL ®): Lower installation cost; Lower operation costAMIT 135: Lesson 6 Grinding Circuit – Mining Mill Operator