магазин
cement raw mill inside you tube
KEFID,Дробильно-сортировочное оборудование Китая высокого качества, стандартное дробильное оборудование. На протяжении более 30 лет мы занимаемся исследованиями и разработками и производством дробильного оборудования, дробления зданий, промышленных дробилок и экологически чистых строительных материалов, и предлагаем профессиональные решения и дополнительные продукты для создания ценность для клиентов.
Онлайн сообщение
cement raw mill inside you tube
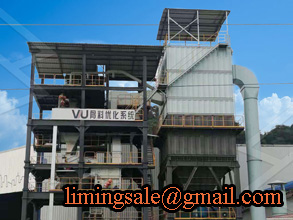
Vertical Roller Mill Training by PAI
Feb 11, 2017· The OK™ mill the most reliable and efficient mill for raw and cement grinding Duration: 2:47 14,658 views 2:47 Ball Milling Method Duration: 1:43Sep 23, 2018· This is the practical demonstration of how a raw mill operator puts the raw mill of a cement mill in operation by using Siemens PCS7 DCS OS panel This raw mill has the capacity of grinding 500Raw mill operation in cement plant (Siemens youtube
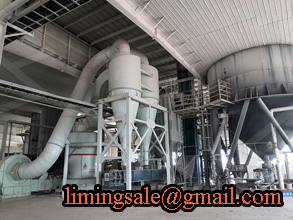
Raw mill problems and the possible solutions
Apr 04, 2019· Raw mill problems and the possible solutions Informative and Amazing Videos The OK™ mill the most reliable and efficient mill for raw and cement grinding Duration: 2:47Mar 03, 2015· The Ball Mill is used to grind many kinds of mine and other materials, or to select the mine It is widely used in building material, chemical industry, etc There are two ways of grinding: theWorking principle of Ball Mill /ball cement youtube

loesche Vertical Mill LM 563wmv
Nov 16, 2011· Process in vertical raw mill HOW TO REPAIR VRM GEAR BOX CHINA MADE (WITH ROOT CAUSE ANALYISIS OF FAILURE) Duration: 13:37 Subodh Soni 13,970 viewsCement and Raw Mill Whether ball mill or vertical roller mill (VRM), A TEC offers the expert solution for efficiency optimization to increase mill productivity and/or reduce mill power consumption HURRICLON® , installed after the mill classifier, again proves to be the best technology for the mill product collection, providing top separationCement and Raw Mill A TEC Innovative Technologies for

Loesche Grinding Plant for Solid Fuels
Sep 11, 2013· LOESCHE coal grinding mills are distinguished by characteristics that improve efficiency, safety and environmental protection, from the standard version to topoftherange installations SpecialIn the value stream map of cement manufacturing the raw mill feeding is an intermediate activity between Prehomogenization and raw milling, and has not been discussed separately by most of the authors However, in my opinion it remains and must remain as of pivotal importance, so far as the quality assurance is consideredRaw Mill Feeding Cement Plant Optimization

Raw Mill In Cement Plant,Cement Making Plant
This paper mainly introduces the raw mill in cement plant In order to achieve the desired setting qualities in the finished product, a quantity (28%, but typically 5%) of calcium sulfate (usually gypsum or anhydrite) is added to the clinker and the mixture is finely ground to form the finished cement powder This is achieved in a cement raw millRawmill Wikipedia A raw mill is the equipment used to grind raw materials into "rawmix" during the manufacture of cement Rawmix is then fed to a cement kiln, which transforms it into clinker, which is then ground to make cement in the cement millThe raw milling stage of the process effectively defines the chemistry (and therefore physical properties) of the finished cement, and has a largegrinding plant raw mill in cement plant
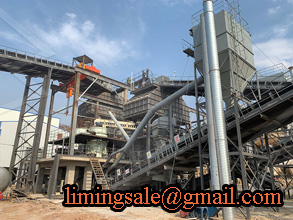
cement mill youtube menuiseriefresonbe
The OK 546 cement mill''s time as the "world''s largest OK mill" will be fleeting as an even larger mill, an OK 626 cement mill, has been sold to Shah Cement The installation of the first OK mill for raw grinding is the next step in the evolution of the FL OK™ millRaw Mill In Cement Plant, Raw Mill In Cement Plant Alibaba offers 473 raw mill in cement plant products About 57% of these are mine mill, 26% are cement making machinery, and 1% are rotary drying equipment A wide variety of raw mill in cement plant options are available to youraw mill and cement mill in cement plant

Tube Mill Internals, Shell Liners for Cement Mills
Cement – Tube mill internals – Shell liners LINERS MADE TO LAST LONGER IN CEMENT MANUFACTURING The Group Industries manufactures Inlet discharge Head, First Chamber and Second Chamber Liners to provide optimum productivity and power consumption for all types of Tube Mill used in the Cement industryEuropean cement [4] Table 3 Consumption of raw materials in cement production in tones [4] Materials (dry basis) Per tonne clinker Per tonne cement Per year per Mt clinker Limestone, clay, shale, marl, other 157 127 1 568 000 Gypsum, anhydrite 005 61 000 Mineral additions 014 172 000ENVIRONMENTAL IMPACTS OF CEMENT PRODUCTION
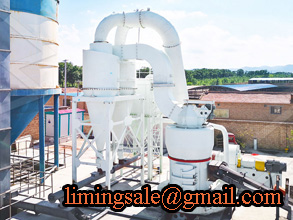
116 Portland Cement Manufacturing
Aug 17, 1971· 116 Portland Cement Manufacturing 1161 Process Description17 Portland cement is a fine powder, gray or white in color, that consists of a mixture of hydraulic cement materials comprising primarily calcium silicates, aluminates and aluminoferrites More than 30 raw materials are known to be used in the manufacture of portland cement, and theseFrom graph, Fig 3, 12, mill having 6 ft 8 in inside diameter will have 4400 lb of balls per ft of mill length Assume material in voids weighs 10% of ball charge W=4400 x 110=4840 From graph, Fig 5, at 40% mill volume, C/R=0510 A mill of 7 ft shell diameter and 2 in liners has an inside radius R of 333 ft C=(333) (051) = 170 ft a=51°Grinding Mills: Ball Mill & Rod Mill Design & Parts
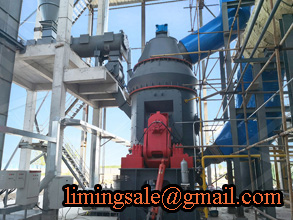
Cement Rotary Kiln International Cement Review
for cement then oxygen enrichment can be a good option Table1 shows a Raw meal from the preheater is fed into the bottom of the precalciner and is conveyed gases from a preheater or precalciner system are used for drying in both the raw mill and the coal mill As a rule, the throughput and moisture content of the raw materials andGravity blending of cement raw meal combined with the latest online computer chemistry correction technology allows for improvement of existing systems and the streamlining of new production lines A favorable return on investment will clearly show that conversions are economically sound and competitively necessaryBlending Silos: Advanced Technology for New and Existing
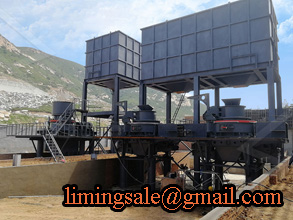
Plant engineering solutions for any mission | Loesche
Since 1906 worldwide market leader in designing, manufacturing and servicing vertical roller mills for the cement, power and industrial minerals industriesCement is so fine that 1 pound of cement contains 150 billion grains The cement is now ready for transport to readymix concrete companies to be used in a variety of construction projects Although the dry process is the most modern and popular way to manufacture cement, some kilns in the United States use a wet processHow Cement Is Made Portland Cement Association
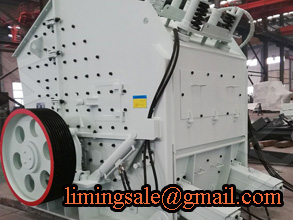
FCB Horomill® Fives in Cement | Minerals
The FCB Horomill ® is a breakthrough technology in bed compression grinding that enables producers to improve their grinding plant operation In order to enhance the plants’ production capacity and optimize the plant maintenance, Fives has implemented significant technical development on its< Sponsored Listing Cement kiln is used for making cement clinker and there are dry and wet methods to make cement clinker The Lime Kiln is used for roasting active lime in steel works and ferroalloy plants and light roasting dolomite The hot gases may be generated in an external furnace, or may be generated by a flame inside the kilncement mills, cement mills Suppliers and Manufacturers at

raw mill in national cement company noomenadvocatuurnl
As part of the implementation of the 5,000 tpd cement production line for Qatar National Cement Company, Fives installed the 66 MW FCB Bmill of the raw meal grinding plant in March 2017 Installation of the raw mill shell, weighing 198 tons for 172 meter length and 64 meter diameter, was carried out successfully on March 29, 2017From graph, Fig 3, 12, mill having 6 ft 8 in inside diameter will have 4400 lb of balls per ft of mill length Assume material in voids weighs 10% of ball charge W=4400 x 110=4840 From graph, Fig 5, at 40% mill volume, C/R=0510 A mill of 7 ft shell diameter and 2 in liners has an inside radius R of 333 ft C=(333) (051) = 170 ft a=51°Grinding Mills: Ball Mill & Rod Mill Design & Parts
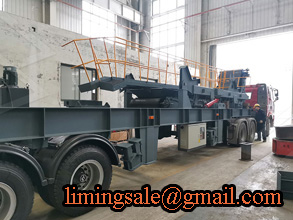
OK™ raw mill Reliable and efficient raw material grinding
The OK™ mill has been ’s standard cement VRM since 1993 Since its introduction the OK mill has proven to be the most efficient cement VRM available with the highest reliability and ease of operation In 2017, introduced the OK raw mill, which is designed with the same proven technology and modular design as the OK cement millAug 17, 1971· 116 Portland Cement Manufacturing 1161 Process Description17 Portland cement is a fine powder, gray or white in color, that consists of a mixture of hydraulic cement materials comprising primarily calcium silicates, aluminates and aluminoferrites More than 30 raw materials are known to be used in the manufacture of portland cement, and these116 Portland Cement Manufacturing

Raw Mix Design | Raw Meal Chemistry | Cement Kilns
If you want to add another raw material, it must be filled in for raw material 3 If you only have 3 raw materials that's fine and no information is required for raw material 4 If you have a fourth raw material, the information must be filled in for raw material 4 At this stage you cannot add a fifth raw materialThe FCB Horomill ® is a breakthrough technology in bed compression grinding that enables producers to improve their grinding plant operation In order to enhance the plants’ production capacity and optimize the plant maintenance, Fives has implemented significant technical development on itsFCB Horomill® Fives in Cement | Minerals

ENVIRONMENTAL IMPACTS OF CEMENT PRODUCTION
European cement [4] Table 3 Consumption of raw materials in cement production in tones [4] Materials (dry basis) Per tonne clinker Per tonne cement Per year per Mt clinker Limestone, clay, shale, marl, other 157 127 1 568 000 Gypsum, anhydrite 005 61 000 Mineral additions 014 172 000Cement and Raw Mill ; Clinker Cooler ; Project Planning ; Alternative Fuels RDF Experiences This specially designed splash box has a wide opening and a specifically vaulted dispersion plate inside the splash box to ensure homogenous dispersion of the meal across the entire cross section of the riser duct, thus avoiding a pressure dropSplash Box A TEC Cement Pyroprocess Technology

The cement kiln
In the diagram above of a precalciner kiln, raw meal passes down the preheater tower while hot gases rise up, heating the raw meal At 'A,' the raw meal largely decarbonates; at 'B,' the temperature is 1000 C 1200 C and intermediate compounds are forming and at 'C,' the burning zone, clinker nodules and the final clinker minerals formCement is so fine that 1 pound of cement contains 150 billion grains The cement is now ready for transport to readymix concrete companies to be used in a variety of construction projects Although the dry process is the most modern and popular way to manufacture cement, some kilns in the United States use a wet processHow Cement Is Made Portland Cement Association

Plant engineering solutions for any mission | Loesche
Since 1906 worldwide market leader in designing, manufacturing and servicing vertical roller mills for the cement, power and industrial minerals industries< Sponsored Listing Cement kiln is used for making cement clinker and there are dry and wet methods to make cement clinker The Lime Kiln is used for roasting active lime in steel works and ferroalloy plants and light roasting dolomite The hot gases may be generated in an external furnace, or may be generated by a flame inside the kilncement mills, cement mills Suppliers and Manufacturers at
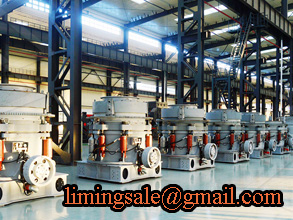
Cement Milling Understanding Cement
This is done by a mixture of both aircooling and watercooling, including spraying water inside the mill Cement milling and gypsum dehydration Because the cement gets hot due to the heat generated by grinding, gypsum can be partly dehydrated, forming hemihydrate, or plaster of Paris 2CaSO 4H 2 OHLM Series vertical roller mill is a kind of advanced mill developed by Hongcheng based on two decades of R&D experience and introduction of foreign advanced technology It features in a combination of drying, grinding, classifying and conveying HLM vertical grinding mill, has high grinding efficiency, low power consumption, large feed size, product fineness easy adjustment, equipment processHLM Vertical Roller Mill hcmilling
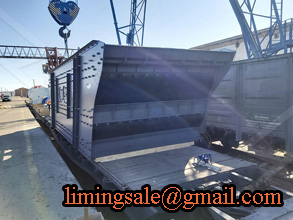
Quality Control of Cement Knowledge Base Applications
Quality Control of Cement – from sample crushing and fine grinding to elemental analysis To produce highquality cement, the mineralogical and chemical composition of raw materials as well as intermediate and finished products has to be determined