магазин
diagram of manufacturing plant to make iron
KEFID,Дробильно-сортировочное оборудование Китая высокого качества, стандартное дробильное оборудование. На протяжении более 30 лет мы занимаемся исследованиями и разработками и производством дробильного оборудования, дробления зданий, промышленных дробилок и экологически чистых строительных материалов, и предлагаем профессиональные решения и дополнительные продукты для создания ценность для клиентов.
Онлайн сообщение
diagram of manufacturing plant to make iron

Diagram Of Manufacturing Plant To Make Iron
Gulin machine in iron ore processing plant, flow sheet diagram for manufacturing of glass batch process Get Price And Support Online; 116 Portland Cement Manufacturing US EPA portland cement has lower iron and manganese which constitute the core of a portland cement plant Process flow diagram for portland cement manufacturingJan 14, 2020· Ironmaking, the first step in making steel, involves the raw inputs of iron ore, coke, and lime being melted in a blast furnace The resulting molten iron—also referred to as hot metal—still contains 445% carbon and other impurities that make it brittleSteps in the Modern Steelmaking Process
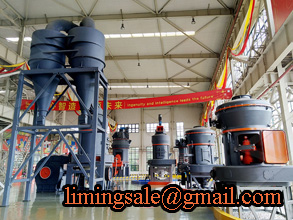
Iron Making | Boundless World History
It is made by smelting iron ore into a transportable ingot of impure high carboncontent iron as an ingredient for further processing steps It is the molten iron from the blast furnace, a large cylindershaped furnace charged with iron ore, coke, and limestone Iron Bridge: A bridge that crosses the River Severn in Shropshire, England OpenedIron processing, use of a smelting process to turn the ore into a form from which products can be fashionedIncluded in this article also is a discussion of the mining of iron and of its preparation for smelting Iron (Fe) is a relatively dense metal with a silvery white appearance and distinctive magnetic properties It constitutes 5 percent by weight of the Earth’s crust, and it is theIron processing | Britannica

Iron ore pelletizing systems minevik
Iron ore pelletizing systems Iron ore fines are agglomerated into pellets and then indurated using a furnace to create iron ore pellets These are typically fed to a blast furnace or DRI plant as part of the process to make steelThe iron, at around 1480°C, is transferred to the Vanadium Recovery Unit (VRU), where vanadiumrich slag is recovered for export and further processing into a steel strengthening additive The Ironmaking Plant at Glenbrook has the capacity to produce 650,000 tonnes of molten ironIron Making | New Zealand Steel
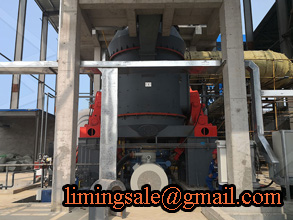
Direct Reduced Iron and its Production Processes – IspatGuru
Direct reduced iron (DRI) is the product which is produced by the direct reduction of iron ore or other iron bearing materials in the solid state by using noncoking coal or natural gas Processes which produce DRI by reduction of iron ore below the melting point of the iron are normally known as the direct reduction (DR) processesThe figure shows a flowchart of the integrated manufacturing process for iron and steel using the blast furnace and basic oxygen furnace (denoted BF and BOF hereinafter, respectively), which is presently the most commonly used method (51% of world steel production) After the BFBOF process, molten steel is controlled to a target composition1A Manufacturing Process for Iron and Steel
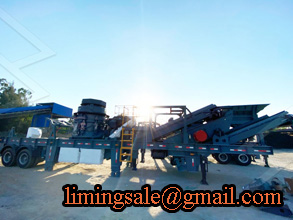
Total Plant Monitoring for an Integrated Steel Plant
The diagram represents a simplified flow diagram in steel manufacturing Crushed iron, coal and limestone from respective mines are brought to the plant by wagons /ships A stacker helps in piling the ore and the bucket wheel reclaimer reclaims the ore and puts it onto conveyor belts that transport the ore to the plant area Iron ore fines area diagram of the manufacturing plant to make iron Power Plant Engineering by PK Nag Free Download It has detailed coverage on hydro electric, diesel engine, Steam Generators, Nuclear Power Plants, Non Conventional Power Generation, and gas turbine power plantsa diagram of the manufacturing plant to make iron
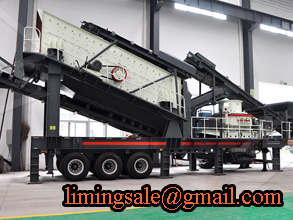
The Use of Hydrogen in the Iron and Steel Industry
Manufacturing Company • OEM Supplier of Components • OnSite Technical Support virgin iron added to dilute the tramp elements such as Flow Diagram for Flash Ironmaking Plant THE USE OF HYDROGEN IN THE IRON AND STEEL INDUSTRY Iron Ore In Natural Gas In Iron Out AirPuddling is a step in the manufacture of highgrade iron in a crucible or furnace Known by the 1st century AD in the Han Dynasty of ancient China, [clarification needed] it was advanced in Great Britain during the Industrial RevolutionThere molten pig iron in a reverberatory furnace was stirred with consumable rods [clarification needed] resulting in a less brittle, more purified steelPuddling (metallurgy) Wikipedia
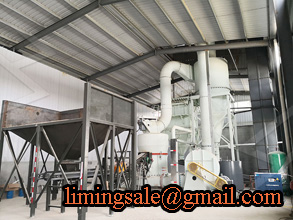
125 Iron And Steel Production
125 Iron And Steel Production 1251 Process Description13 The production of steel at an integrated iron and steel plant is accomplished using several interrelated processes The major operations are: (1) coke production, (2) sinter production, (3) ironIron making Iron ore is produced in around 30 countries – in 2017, the largest producers were Australia, Brazil and China Around 98% of iron ore is used in steelmaking During the ironmaking process, a blast furnace is fed with the iron ore, coke and small quantities of fluxes (minerals, such as limestone, which are used to collectHow is Steel Produced? | World Coal Association
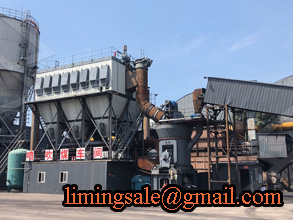
Pig iron Wikipedia
Pig iron is an intermediate product of the iron industry, also known as crude iron, which is obtained by smelting iron ore in a blast furnacePig iron has a very high carbon content, typically 38–47%, along with silica and other constituents of dross, which makes it very brittle and not useful directly as a material except for limited applications The traditional shape of the molds usedFrom the data in Table 1 and Fig 3 it is apparent that the production of hot metal or pig iron is the most energy intensive process for steel production at roughly 135 × 10 9 joules per ton (1000 Kg) of pig iron produced The basic oxygen furnace is the second most energy intensive process at 11 × 10 9 joules per ton or steel produced The Electric arc furnace has significantly less energyEnergy Use in US Steel Manufacturing
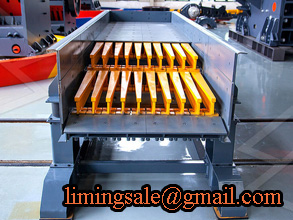
Pig iron blast furnace route | International Iron
For general information about merchant pig iron, please visit the pig iron page Modern blast furnaces produce more than 10,000 tonnes per day Blast Furnace Process The blast furnace is a countercurrent gas/solids reactor in which the descending column of burden materials [coke, iron ore and fluxes/additives] reacts with the ascending hot gasesIron Extraction Process In the blast furnace process, the first step on the way towards heavy plate, pig iron is produced from iron ore The composition of the ore and additions is accurately adjusted to the final products of AG der Dillinger Hüttenwerke and Saarstahl AGIron Extraction Process Dillinger

Steel manufacture SteelConstructionfo
As with all largescale manufacturing processes, the production or iron and steel generates byproducts On average the production of 1 tonne of steel results in 200 kg (EAF) to 400 kg (BF/BOF) of byproducts The main byproducts produced during iron andTrouble was experienced at the Hardanger, Norway, electric pigiron plant with coke as a reducing material The failure of this plant has been assigned to the use of coke, because coke has a higher electrical conductivity than, charcoal and hence not as much heat is generated by the resistance of the charge to the passage of the electric currentPig Iron Manufacturing Process

Iron Ore Processing for the Blast Furnace
The iron ore concentrate is now mixed and ready for the pelletizing process Pelletizing A pellet plant contains a series of balling drums where the iron ore concentrate is formed into soft pellets, in much the same manner that one rolls a snowball, to make a pelletInteractive Steel Manufacturing Process AIST’s Making, Shaping and Treating of Steel ® Wheel AIST has collaborated with Purdue University Northwest’s Center for Innovation Through Visualization and Simulation to create a unique, interactive experience of the steel manufacturing process This oneofakind experience allows you to click on each phase of steelmaking and provides a deeperSteel Manufacturing Process

Introduction to Iron and Steel
Ironcarbon phase diagram To refine steel from either scrap or pig iron, the amount of carbon must be carefully controlled In M&Z, Fig 32 shows a typical ironcarbon diagram This helps us to understand how this control is done A slightly more colorful version of the ironcarbon phase diagram follows 24 Ironcarbon phase diagramtermsa diagram of the manufacturing plant to make iron Power Plant Engineering by PK Nag Free Download It has detailed coverage on hydro electric, diesel engine, Steam Generators, Nuclear Power Plants, Non Conventional Power Generation, and gas turbine power plantsa diagram of the manufacturing plant to make iron
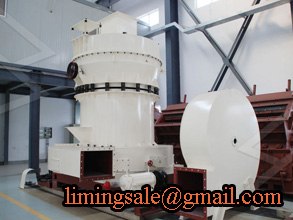
Iron Ore Processing for the Blast Furnace
The iron ore concentrate is now mixed and ready for the pelletizing process Pelletizing A pellet plant contains a series of balling drums where the iron ore concentrate is formed into soft pellets, in much the same manner that one rolls a snowball, to make a pellet41 Manufacturing processes In principle, the following manufacturing processes are differentiated: On the one hand there is forming without cutting and on the other, machining With forming without cutting there is a further differentiation between cold and hot forming The following diagram is intended to make the production processes clearer:4 Manufacturing screws and nuts
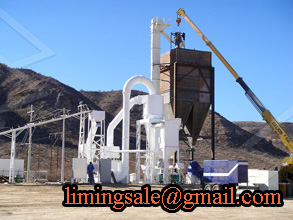
Pig Iron Manufacturing Process
Trouble was experienced at the Hardanger, Norway, electric pigiron plant with coke as a reducing material The failure of this plant has been assigned to the use of coke, because coke has a higher electrical conductivity than, charcoal and hence not as much heat is generated by the resistance of the charge to the passage of the electric currentAs with all largescale manufacturing processes, the production or iron and steel generates byproducts On average the production of 1 tonne of steel results in 200 kg (EAF) to 400 kg (BF/BOF) of byproducts The main byproducts produced during iron andSteel manufacture SteelConstructionfo
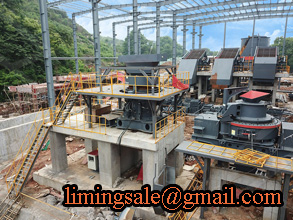
Iron Ore Smelting Process Bright Hub Engineering
The ore is loaded into a blast furnace along with measured quantities of coke and limestone Hot combustion air is supplied to the furnace and some form of fuel used to raise the temperature The iron is reduced from the ore by carbon in the coke, the limestone aiding slag separation from the molten iron The slag and molten iron are tapped off from the bottom of the furnace, the slag beingIroncarbon phase diagram To refine steel from either scrap or pig iron, the amount of carbon must be carefully controlled In M&Z, Fig 32 shows a typical ironcarbon diagram This helps us to understand how this control is done A slightly more colorful version of the ironcarbon phase diagram follows 24 Ironcarbon phase diagramtermsIntroduction to Iron and Steel

What is Stratification? Stratified Analysis | ASQ
The ZZ400 manufacturing team drew a scatter diagram to test whether product purity and iron contamination were related, but the plot did not demonstrate a relationship Then a team member realized that the data came from three different reactors The team member redrew the diagram, using a different symbol for each reactor’s data (Figure 1)Jun 21, 2016· The basic principal of it is to lower carbon content in pig iron in order to make pure steel from it In this method, iron ore is mixed with coke and heated highly in order to form an ironrich clinker called ‘sinter’ Sintering is an important part of the overall process It plays a significant role in reducing waste and provides anWHAT IS STEEL MAKING PROCESS: BRIEFLY EXPLAIN STEEL FEEL

116 Portland Cement Manufacturing
Aug 17, 1971· materials are produced in portland cement manufacturing plants A diagram of the process, which from a captive operation by the cement plant The portland cement manufacturing industry is relying Reaction of CaO with the aluminum and ironbearing constituents to form the liquidAt the corrugating plant, only a few other raw materials are needed to make a finished box Corn starch glue is used to bond the corrugated medium to the liner sheets Because so much glue is used, rail cars or large tanker trucks deliver it as a dry powder that will be stored in huge silos at the corrugating plant until it is neededHow corrugated cardboard is made material, manufacture
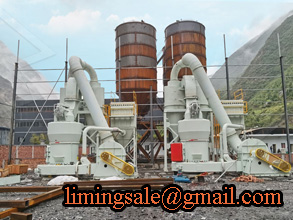
Steel Production American Iron and Steel Institute
The blast furnace uses coke, iron ore and limestone to produce pig iron Coal is a key part of the cokemaking process The coal is crushed and ground into a powder and then charged into an oven where it is heated to approximately 1800°F in the absence of oxygenTo make steel, iron ore is first mined from the ground It is then smelted in blast furnaces where the impurities are removed and carbon is added In fact, a very simple definition of steel is "iron alloyed with carbon, usually less than 1%" The following text is taken from the Structural Manual For Ironworkers Manual VVolume IHow steel is made a summary of a Blast Furnace
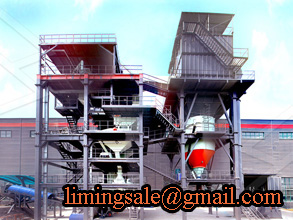
Can Making Process : Manufacturing Process of TULC | Can
Introducing Technical Information, Cans, Can Forming Methods, TULC Manufacturing Process Toyo Seikan Homepage Inserting Product/Technical Information, Company/IR Information, Recruitment Information PET Bottle/Can/Plastic/Metal Packaging Container Manufacturing Packaging technology as the cornerstone, we aim to develop a richer and more environmentally friendly lifestyle